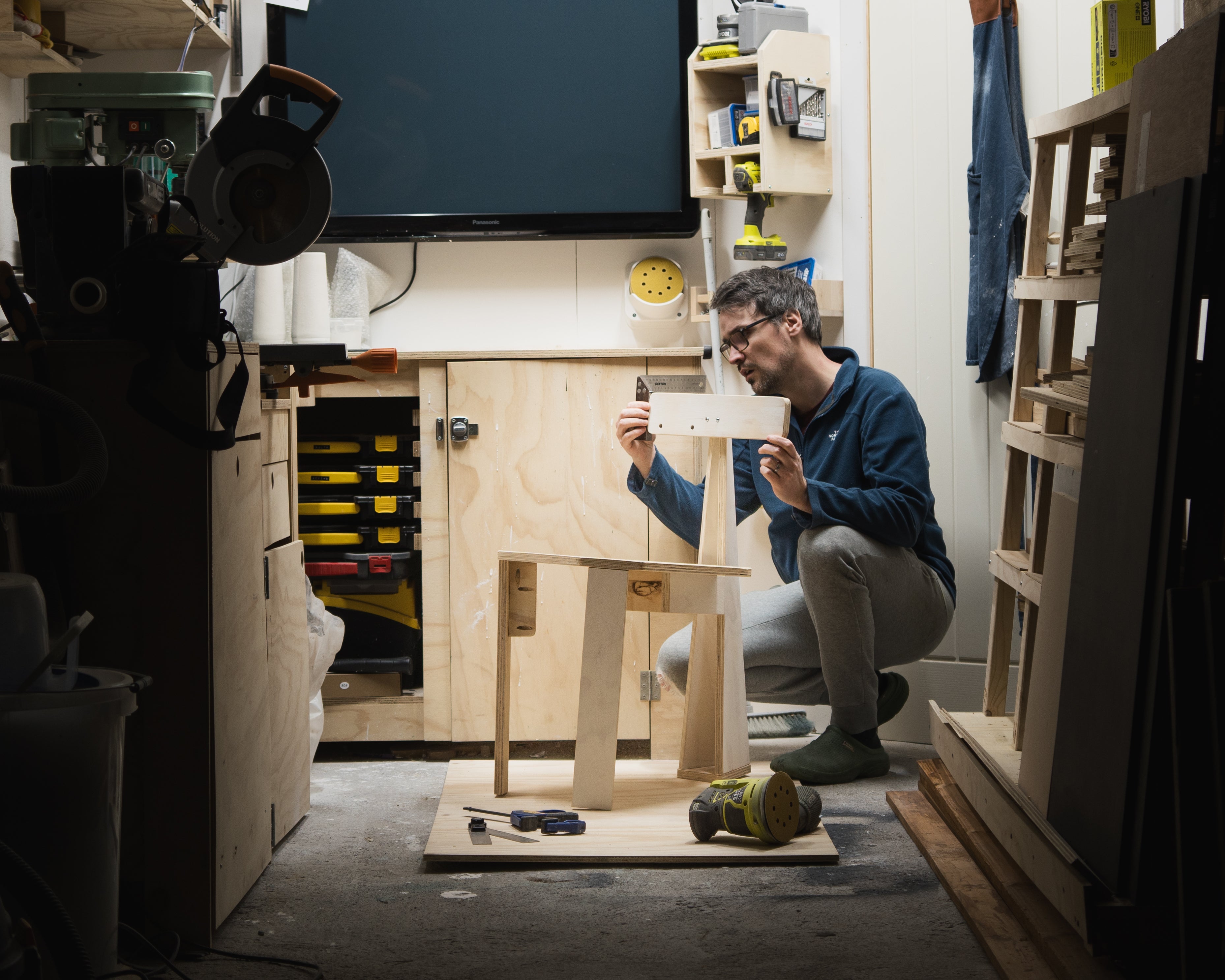
Tall Ships Maker - Introducing Ben Durack
Share
Ben Durack, with his background in commercial product design and experience in digital fabrication, tells us about his Tall Ships project, from VR to 3D printing and beyond...
Hi, I’m Ben, a full-time design educator in Aberdeen, Scotland and independent product designer. I’m delighted to be part of the Tall Ships Makers Program alongside some very talented makers. As a practising product designer, my practice centres around creating products that surprise and elevate honest materials. I am a hands-on maker, blending traditional analogue making processes with cutting-edge digital tools (3D modelling in VR, digital fabrication, AI) to push the boundaries of what is possible with batch production.
Having lived in Aberdeen for over a decade, I have worked across a wide range of design roles from design consultancy to running an open access digital fabrication studio in the city centre. My journey has included co-founding a startup focussed on redefining plastic waste in the city, as well as designing and putting into production my own products, which are uncompromising in every aspect. Alongside this, I currently teach full-time on the Product, Ceramic and Jewellery course at Gray’s school of art. If there’s one constant in design, it’s change. Learning to be comfortable feeling uncomfortable has been one of the most powerful lessons learned over my career – embracing change and always striving to expand my skillset, be it analogue or digital.
When I discovered the Tall Ships Makers Program I was immediately excited about the prospect of pushing my practice into new territories, drawing on our current and historic relationship to the sea through Aberdeen’s ship building heritage. The craftsmanship and innovation behind the evolution of shipbuilding, from 18th-century wooden vessels to 20th-century steel ships, offers a wealth of material and narrative possibilities. When looking back at Aberdeen’s long history with ship building I was drawn immediately to the tea clippers, an incredible period starting in the 1840’s and lasting only a few decades before steam power took over. The demand for tea, resulted in the fastest sail ships ever made. This developed into the annual tea race, where ships set sail to bring back the first harvest from China to London with the winner being able to sell their tea at a premium.
AI video created from the iconic painting of the Thermoplae by Tim Thompson.
The Thermoplae (built in Aberdeen) is still the fastest sail ship to date. When I grew up imagining pirate ships, this is what I thought of… infinite number of sails, huge bow and incredible wooden craftsmanship. The essence of the tea clipper and the history of the Thermoplae is something I want to be able to celebrate – honouring the past while inspiring the future.
As a product designer, I have developed an extensive network of manufacturing partners over the years and this is something I wanted to really highlight in this project. We have an incredible manufacturing industry in the North East, ranging from Highland Heritage Woods who source and process local timber to Reekie Steeltec who can provide an end to end service with metal from laser cutting and folding to powder coating.
I am always embracing new tools, constantly looking for opportunities to incorporate these new tools meaningfully into my design process. As an early adopter of Gravity Sketch (3D modelling in virtual reality) this was the perfect project to really embrace this tool. Modelling at a 1:1 scale, I was able to explore nearly 100 different designs and make purposeful design decisions. Following a broad approach to early ideation, I then meticulously evolved a design direction I thought had potential, 3D printing countless iterations at 1:4 scale, working closely with my industry partners and making rough 1:1 scale prototypes to test comfort.
Eventually, a range was developed that I feel fully embodies my ambition to showcase the magic of the Clippers built in Aberdeen:
- Celebrate local industries
- Showcase craftsmanship
- Be a statement
- Create a sense of wonder
- Testament to the region’s heritage
- Celebrate sustainable design practices
- Innovative materials
During its time, the Thermoplae was considered “experimental” because of its innovative design and composite use of metal and wood. While being innovative was celebrated at the time, being labelled “experimental” was not. Throughout this project I seek to embrace the qualities that made the Thermoplae “experimental”, wearing this as a badge of honour.
We are a city, and a people who have been shaped and honed by the crashing
waves of the North sea. Our lives and livelihoods are rooted in this maritime
heritage, which has grown and adapted throughout the passage of time; a city built
on trade, proud ship builders, strong fishing families, and in more recent history, a
city of oil. Even now, as these industries move and adapt, we still feel the call of the
water, a resilient city salted by an often unforgiving tide.
Find out more about Ben's practice at www.bendurack.com/
Follow Ben on Instagram here